The voting for new inductees to the Mountain Biking Hall of Fame has begun for 2017. Several very qualified parties have been nominated including the great frame designer Brent Foes and legendary racer Steve Peat. This is a year with some strong contenders. Among them, Mark Norstad. To many, his name may not come to mind. To others he is the glue that binds much of an industry. You probably don’t know his name because self-promotion isn’t a goal of his. I strongly support a vote for Norstad this year. If you’ve ever owned a custom handmade bike, you may want to do the same.
I am a customer of Mark’s and I have known him for at least 20 years and of him for almost 30 years. Without the parts I buy from him, my bikes would be much harder and more expensive to make. I learn about design when I look at his work. That informs my work. That’s my personal testimonial about how his work directly effects me.
Audio Interview from NAHBS 2017:
Mark Norstad should be inducted to the Mountain Biking Hall of Fame due to Mark’s historic and continuing contributions to the machines we ride; how they have developed, and how they continue to take form. In Mark’s own words, “I make products that allow frame builders to build the bikes that advance frame building. That’s been true since 1983, and is still applicable today.”
Mark started Paragon Machine Works in 1983 as a small machine shop in his parent’s basement in Corte Madera, CA (Marin). Today, Paragon Machine Works is the largest supplier of high-end frame building parts in the world occupying an 8,000 sq. ft. facility in Richmond, CA. His frame building parts dominate in an industry full of very creative people and his design fingerprints are on almost all of the custom high-end bikes produced around the world.
In his youth during the 1970s, Mark was using his bike to explore Marin County’s trails from his home in Corte Madera, modifying his own bikes, and learning industrial arts. In the third grade, he got his first bicycle, a Montgomery Ward cruiser that was too big for him. By the eighth grade in the mid-1970s, he was cutting that same bike apart to see how it was put together, lacking any real mechanical knowledge. While attending Redwood High School, he started taking machine shop to learn about metal fabrication and machining. This was a different time when a career in the metalworking industry was a legitimate pursuit for a young person. Other math and drawing classes furthered his depth of understanding of engineering. All the while, he was scouring the dump for old bikes, cutting and modifying them to last and work better and riding the trails of Marin. The durability of the old mild steel bikes was a constant problem and required constant improvement. Moving on to more serious study of the industrial arts at the College of Marin in Kentfield, with Joe Breeze in the class before him and working on building his first mountain bicycles, Mark’s eyes opened to what other people in the county were doing. Graduating, and working as a professional machinist, Mark explored what could be done with automobiles and other projects but never losing his love of bicycles. After going back to school to round his learning off with art, sculpture, and liberal arts classes and after encouragement from a former employer, Mark bought his own (brand new!) machines and started his own shop in his parent’s basement.
With Mark in Corte Madera and the Koski brothers and Mert Lawwill in just next door town of Tiburon, one of Mark’s first ‘for hire’ bicycle projects was to make the front dropouts and a pair of prototype sets of rear dropouts used for Don Koski’s (Cove Bike Shop) ‘Trailmaster’ bikes. As those bikes circulated in the market, so did the interest in the sport of mountain biking. Soon, Eric Koski (Don’s brother) and Norstad were sharing space in a Greenbrae shop. This was a pivotal time in the development of these evolving bikes and Mark was intimately involved.
Mark had been a customer of the Cove shop before that, though, buying parts for his own creation. Handbrake levers come to mind for a 1979 3 brake bike of Mark’s. Front drum, rear coaster and disc. Everyone was trying something then. Nobody knew what was going to work best or in what conditions back then. Mark was experimenting but he was a couple years younger than the Fairfax guys and working essentially alone. Every now and then talking with the Fairfax guys or the Larkspur Canyon Gang about what was working and what wasn’t. Everyone had something to try. The group of people that surrounded him would go on to become infamous in the late 1970s and 1980s; Breeze, Lawwill, Slate, Potts, Gordon, Cunningham, Helfrich, and a host of others. It was a time when American bicycle frame building was in its infancy and the possibilities of what became the modern mountain bike were just being figured out.
The conflux of location, timing, and a lot of hard work led to Mark producing and designing most of the special parts used to fabricate many primordial mountain bikes and later, also, many of the parts used on these bikes by champion riders. Mark’s success, and what he gave this new fledgling industry, was mostly due to his understanding of the economics of bicycle manufacture: margins are low on bicycle frames but to make them well a builder needs special and custom parts in small batches at very low prices. This is not an easy task but it is at the heart of what makes it possible for builders to do what they do. Mark’s constant struggle is allowing for the constant evolution of the bicycle to be better than it had been.
Often, Mark might not be the originator of an idea or need within the industry. Either a parts manufacturer, like Shimano or SRAM, will introduce a new part according to a self-established standard or a builder will come up with a specific idea on their own. Shimano works closely with Mark to ensure that smaller builders will adopt their products and will give information to Mark so he has the needed frame parts available when Shimano’s parts are released. Mark will then be tasked to, essentially, act as engineer for them. Inventing methods and processes that will get the results required. In the past 35 years, this has been a big part of Mark’s job. Make ideas actually happen and cash checks doing it. He’s also known for doing this without ego. Without forcing his name to the front. He lets others take their credit. His customers know who he is but their customers don’t. Most people don’t know his name.
He helps framebuilders work profitably. His steerer binder and handlebar binder parts make it so a builder can cut the two ends of one tube, make two welds, and have a completed custom high end stem. No need for setting up and welding binder bosses in six more positions. This helps his customers succeed and that is good business.
A case of this is in the late ninties where Hayes had released a chainstay mounted disc caliper. The industry needed a way to use this. Staying with the requirements for the caliper position, Mark produced and inexpensive part to make this happen as well as a fixture and instructions so basic framebuiders could do it.
Titanium is the first metal people will think of when they think about Paragon Machine Works and really put it on the map. Since first being contracted by Gary Helfrich, a co-founder of Merlin Metalworks, in the mid-eighties to produce parts from the material for bicycle framebuilders, Mark’s catalog has only grown and he has become the near-sole source of titanium framebuilding parts in the world. From that day, Paragon has been the name behind getting a titanium frame made outside of China. Sandvik and Ancotech, the leading distributor of 3/2.5 titanium tubing to frame builders were sending business to Mark for 6/4 and CP titanium parts. The chances are, if you’ve owned a titanium bicycle, Mark made and maybe designed the parts used to make it.
When designing a part, Mark will focus on manufacturability at the outset. Each feature and engineering necessity of a dropout, head tube, or any of the multitudes of parts he now makes will be described in ways that reduce manufacturing cost, time, and build quality and structure to the part. They work well, look good, and most importantly, they are economical in an industry that is very price sensitive. Very few shops are able to do this and Mark has been doing it for a very long time.
1986 was the year that Paragon went to CNC machining with a computer controlled lathe. Then, the bike business tended to use Mark for turned parts and Dave Garoutte (DKG, San Rafael, CA) for CNC milled parts. In 1992 when Mark obtained a CNC mill. The Fat City Cycles 10th Anniversary frame dropouts were made on this mill that year. Soon, Mark was doing almost all of the CNC work for the high end frame industry.
During the era of cantilever and v-brakes, it was Mark that developed a screw in boss for framebuiders to take advantage of the new posts that would screw into the new aluminum and magnesium suspension fork lowers. In steel or titanium, right away, it was the standard for how a high end bicycle mounted front and rear brakes.
An interesting solution to the problem of belt drives on bicycle led to Mark’s development of the ToggleDrop dropout. To allow for easy wheel removal when the wheel doesn’t just need to be placed but highly tensioned, a more complex solution was required. This added quick tensioning and de-tensioning of the belt to wheel removal. It’s patented and nothing works better.
The singlespeed mountain bikes were made remarkably better for us because of Mark. His sliding dropouts were based on a rough design of Eric Baar’s. With disc brake mounts made easy with the chain tension, these quickly became the standard interface. Now, a rocking option, also by Paragon and based on a design by Todd Ingermanson of Black Cat Bikes is available. In both these cases, the design originator had a good idea but couldn’t meet manufacturing goals. Mark could improve the design and produce them in mass and in high quality. Everyone benefited and singlespeed disc bikes became a real thing.
T47 is a recent place where Mark made a huge difference to the industry. Several companies were working on a way to use 30mm spindles in a threaded bottom bracket shell that was good for both titanium and carbon builder. Many builders don’t like press fit bottom brackets. When Chris King and White Industries came to Mark separately with similar but different designs, Mark stepped to the two and negotiated a common solution. Left to their own, a split standard would have ruined the concept. With an agreed standard, we all benefit. Thanks Mark!
Mark has made components as well. In 1988, Mark produced 50 pair of 135mm and 140mm (WTB) PMW hubs for mountain bike use to add to a full line of high end titanium bottom bracket spindles with quality bearings and aluminum cups. He made 30 steel quill stems in the late eighties followed by some titanium quill stems. Titanium chainrings for Road World Champion Gianni Bugno’s training bikes. Jimmy Deaton’s gigantic 66 tooth chain ring used to win at the Mammoth Mountain Kamikaze race. Also, some 1992 US Olympic track race bikes saw some Paragon dropouts and bottom brackets. The plastic bodies for the WTB MP-250 Stealth clipless pedals were cut by Mark.
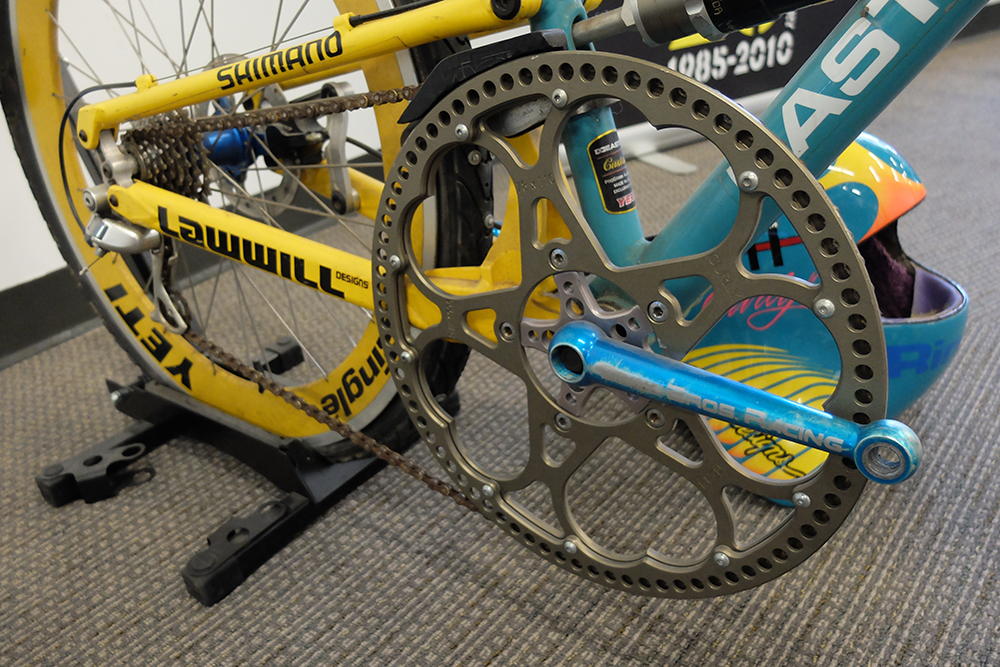
The 78-tooth chain ring for 1997 122 mph speed record champ Carolyn ‘Curly’ Skyer.
Mark worked with Mert Lawwill from 1994 to 1999, once again, sponsoring the Yeti/Schwinn racing team of the late nineties with frame parts and chainings. Mark made many of the frame parts on these race bikes including the patented dropout parts. They pushed the envelope and made huge moves in progressing what a downhill bike would eventually become. This team was dominant and driven to win and they had some of the best hardware around…and World Champion Jürgen Beneke was on one of the bikes.
On the floor of the North American Handmade Bike Show, almost every metal bicycle will be using a Paragon part of some type, often every machined part on the bike frame will be from Paragon. Mark’s presence is ubiquitous in this world of wonderfully hand crafted machines. Trends start with these bikes and Mark is the first person called on to help make it possible to do new things.
The parts that Mark produces don’t just help professional frame builders. Hobby builders and even university students, like those enrolled in the University of Iowa Hand Built Bicycle Program, use his parts to make their own special dreams come true. Because the economic hurdle of the costs for developing and production for the parts have been amortized, novice builders have access to a catalog of professional working parts for their frames. The result of this is an environment where any rider can show up on a local ride on a bicycle that they built themselves, and it will be a very nice bike. Anyone with a bike idea can get started thanks to Mark.
As things tend to go full circle, today, Mark is once again working on chassis parts for Mert Lawwill’s StreetTracker motorcycle and Mert’s MertsHands prostetic arm. The arm is incredible, allowing easy connect and disconnect for bicycle and motorcycle for riders who are amputees. While it is Mert’s project, Mark contributes with his manufacturing and engineering details that make this project a reality. The arm is electronically controlled for a variety of conditions, won’t break, and performs well. Mark is making arms so people can ride bikes.
As an employer, Mark employs 8 full-time employees to run and manage the CNC and manual machine tools that cut the metal in his shop. Over the past 34 years, these employees have gone on to make their own mark in the mountain bike culture and sport. This is a legacy that only grows exponentially as the lessons he teaches get taught to another generation further down the line.
Just 1/3 of Paragon Machine Works work comes from outside of the bicycle industry. Bicycles are his company’s priority and what keeps it going during the hard times.
Mark is Co-Dictator for Life of the Society of People Who Actually Make Their Own Shit (SOPWAMTOS). A group that he and Bruce Gordon have curated since the second or third Eurobike Expo to celebrate work sold by people that actually produce it, strange awards, and classy fez hats. In the early days, the awards celebration was held on the floor of Interbike. Later, when things were getting out of control and the party got to big, they were kicked out of the venue. Unstoppable, they continued to take over a Las Vegas motel parking lot. Today, SOPWAMTOS is a staple of NAHBS party scene. Hijinks and goofing around are a priority to last in the bike industry. Mark also keeps it fun, having made a six person rail bike just to goof around.
Paragon Machine Works has co-adopted the Downie River Trail in the Plumas National Forest near Downieville, CA with Paul Component Engineering through the Sierra Buttes Trail Stewardship. This helps ensure that great singletrack stays available in one of the nicest places to ride in California.
Lastly, PMW donates ALL revenue from our promotional parts (T shirts, Bottle Openers, Socks, etc.) to bicycle related non-profits. Total is over $15,000, and has benefited over 20 organizations.
Paragon Machine Works is a proud member of:
Bike East Bay
Friends of China Camp
Friends of Tamarancho
Marin County Bicycle Coalition
Marin Museum of Bicycling and Mountain Bike Hall of Fame
National Interscholastic Cycling Association
San Francisco Bicycle Coalition
Sonoma County Bicycle Coalition
_____________________________________________________________________________________
Testimonials:
Mark Slate-
Mark Norstad is a man that can make stuff. That’s a valuable commodity and rare in Marin County where we both have lived a long and privileged existence. With machinery and skill and can-do attitude he has turned out some very unique parts. Always willing to help or say “I can’t be competitive making that” when asked. If you look at what he has offered from the enterprise known as Paragon Machine Works you will notice two things. One is a particular style, a form of robust engineering art. The second is that his offerings are like none other. That’s evolution for you. Mark knows where he can excel. Over the long course of his career he has made many things. It has always been clear to me that he does what he wants from a very pure place in his soul and that turning a profit is important but the joy of fabrication is number one. A man with an opinion and not afraid to use it, a recent conversation we had about the purity of the bicycle (I was touting electric) left me with no doubt of his personal feeling for the bicycle, the kind you have to pedal hard to go fast. Many people in the world of bikes know Mark. He has been around, and around, like a wheel that cannot be stopped. The man has Momentum. It seems only fitting that he be recognized for his achievements and spirit by the Mountain Bike Hall of Fame. Not only fitting be deserved. Whatever comes he will always be a man worthy of respect in my eyes. He makes stuff with his own machinery. That is a rare claim. And he makes a living doing it. Awesome, in the truest sense.
Steve Potts-
Hi all at the MBHF,
My earliest memory of Mark is his little shop at his parents’ house making parts as a small job shop. Mark made our first titanium drop outs for my bikes and of course did a perfect job, and this led to more and more bike parts from Mark. To this day, Mark , Donna and the crew at Paragon Machine is literally a part of my entire bike building life and any success I have had is directly related to Mark’s dedication to the bike industry…period, not to mention Mark is truly one of the most stand up people I know! He has consistently, quietly listened to what is needed in the industry and has always seemed to be a step ahead due to his hard work, no sooner than anyone thinking about a new part that we need, Mark usually is already making it or it is already on the shelf ready to ship. Mark is truly connected to the roots of the Mountain Bike! Thanks Mark!
Mert Lawwill-
To whom it may concern
I am writing in support Mark Norstad to be inducted into the Bicycle Hall of Fame.
I first met Mark back in the 90’s when he was a sponsor for the Schwinn/YETI mountain bike racing team. We won the World Championship in 1998 with Jurgen Beneke and several riders like Elke Brutsart and Marla Streb who won several World Cup downhill events using parts he made. He was a steady supplier of parts and supplies for the team. He helped with making any special parts like what we needed for Carolyn “Curly” Curl special bike when she set the world downhill speed record at 115 MPH on ice in Switzerland back in1998. I believe the record still stands. I have worked with Mark since then making parts for my motorcycles and prosthetic arms for bicyclist and motorcycle riders missing hands and arms. He has always been a pleasure to work with and is making parts for me at this time. I speak very highly of the integrity of this man.
Ross Shafer-
4/3/17, To Whom it May Concern,
I would like to add my comments to the others you’ve received regarding Mark Norstad’s MTB Hall of Fame nomination.
For a long time, Mark has been supporting the needs of mountain bike frame builders and innovators by producing some of the finest frame components and tools ever made. His dive headlong into the world of titanium frame components opened up the possibilities for so many builders interested in the use of that material.
Perhaps his biggest contribution has been that of staying on top of the industry’s ever changing fashions and standards. This has been an immense help to the smaller builders of the world who simply do not have the wherewithal to design and produce components that are compatible with the new components and standards that seem so prevalent in the modern bike industry.
Mark’s dogged determination to stay on top of this has required close work with Shimano a company that has long recognized Mark’s importance amongst his frame building customers.
Mark’s chosen path within the bicycle industry has been one of great benefit to far more people than those who know who he is. Those of us who know and appreciate his talent and skills have long considered him a highly valued source and ally. Besides all that he’s a dang nice guy too!
Best of Luck to Mark for his potential induction to the MTB Hall of Fame.
Charlie Cunningham and Jackie Phelan-
Mark Norstad embodies the spirit of inventiveness and dedication that made the early days of mountain biking so rich and creative. He mastered machining at a time when the USA closed down almost all the manufacturing done domestically. He brought well-thought out components to his avid buyers, and we have personally benefitted from his generosity in many ways.
Paul Price, Paul Components-
I would strongly recommend Mark Norstad as an inductee into the MBHOF. There are bike frames and then there are BIKE FRAMES. For the later custom handmade variety there is only one source for bits, and that is Mark Norstad’s Paragon Machine Works.
For a genre to advance innovators need to experiment and replicate. For frame builders it doesn’t take very much experimentation for Mark to get on board with pieces that allow for replication. He’s been at the fore front of advances in frame technology for many years. He was in on the heyday of the early mtb and is in on the advancement of the technology as it is today.
As a side note I would also add he is one of nicest guys ever and is always open to discussing anything bike related.
Cameron Falconer-
As a small frame builder Mark Norstad and Paragon Machine Works is a huge part of what makes my job possible. Having a supplier of high quality American made fittings who is also a wealth of knowledge is a great help. Marks parts are outstanding and highly functional; if it came from Paragon you can count on it being right. Mark listens to his customer base and helps keep us small builders current by making new widgets to keep up with ever evolving options in frame standards. Without PMW my job would be more difficult, less satisfying and not nearly as fun.
Matt Hebberd-
I would like to add my comments regarding Mark Norstad’s MTB Hall of Fame nomination.
Since 1983 Mark has been machining unique bicycle parts. He started before that by making himself, his brothers and friends replica Bendix front hubs that were hard to find for our klunkers. In the early /mid-eighties as the Northern California mountain bike scene was taking off, builders like Steve Potts, Charlie Cunningham, Otis Guy, the Koski brothers, Tom Ritchey, Keith Bontrager, Ross Shafer, Bruce Gordon, Scot Nicol and Jeffrey Richmond all used Mark as the “go-to-guy” for their unique machining needs. For several years he machined all of WTB’s grease guard hubs.
By the early 90’s as the titanium trend began, Mark was the guy to go to for Ti drop-outs and bottom brackets and anything else made of titanium for a bike. Mark was a frame builders dream. Framebuilders simply can’t afford to design and machine their own dropouts, brake mounts and other small parts. That’s where Mark comes in. He produces more than 150 kinds of dropouts and dropout parts, 100 kinds of cable stops, 45 bottom bracket shells, 40 head tubes, 36 brake mounts, 20 derailleur hangers, 36 framebuilding tools, 13 stem parts … and of course, multiple kinds of bottle openers. And all of his products go to framebuilders and on bikes that are built and ridden in countries around the world.
Mark’s latest ride through the bicycle industry has keep him working closely with today’s top frame builders as well as Shimano, who has always recognized his importance among worldwide frame builders.
From someone who has known Mark since I was a young kid cruising my klunker with him and his brothers and witnessed his contribution to the cycling world, his nomination into the Mountain Bike Hall of Fame is way overdue.
Outside Links and Reference:
http://www.paragonmachineworks.com/
_____________________________________________________________________________________
The list of large companies that have worked with Mark or purchased his parts goes on longer than can be listed here. A few worth mentioning are:
Select Current Customers of Paragon Machine Works:
Anvil
Argonaut
Baum
Black Cat
Black Sheep
Boo
Chris King
Cyclo-Cross World
Dean
Easton
Easy Racer
Ellis
Engin
Enigma
Enve (Edge)
Eriksen
Firefly
Francis
Funk
Hampsten
Holland
Hunter
Independent Fabrications
Jones
Kirk
Kish
Kocmo
Koski
Kualis
Landshark
Lawwill
Lynskey
Marinoni
Moots
NTP
Paketa
Parlee
Pass + Stow
Paul
Potts
Quiring
Reeb
Renovo
Reynolds UK
Rock Lobster
Ross Schafer
Santana
Seven
Sinewave
Soulcraft
Spurcycle
Sputnik
Steelman
Strong
Sysip
Vanilla
Vertigo
Viscous
W.H. Bradford / Nemisis / Hodges
White Industries
Wolf Hound
Select former Customers of Paragon Machine Works:
Bianchi
Boulder Bicycles
Castellano
De Rosa
DKG
DT Swiss / Hugi
Eisentraut
Fat City Cycles
Fischer Bicycles
Funk Cycles
Grafton
GT Bicycles
Guru
Helfrich
Huffy
IBIS
Jericho
Kelly
King Cage
Kona
Litespeed
Marinovative
Mongoose/Brunswick
Mountain Goat Cycles
One-Off Titanium
Otis Guy
Paul
S&S (1991 Coupler)
Salsa Cycles
Sanvik – Ti Sports Division
Schwinn/Lawwill/
Yeti
Spectrum
Trek/LeMond Bicycles
White
Wilderness Trail Bikes (WTB)